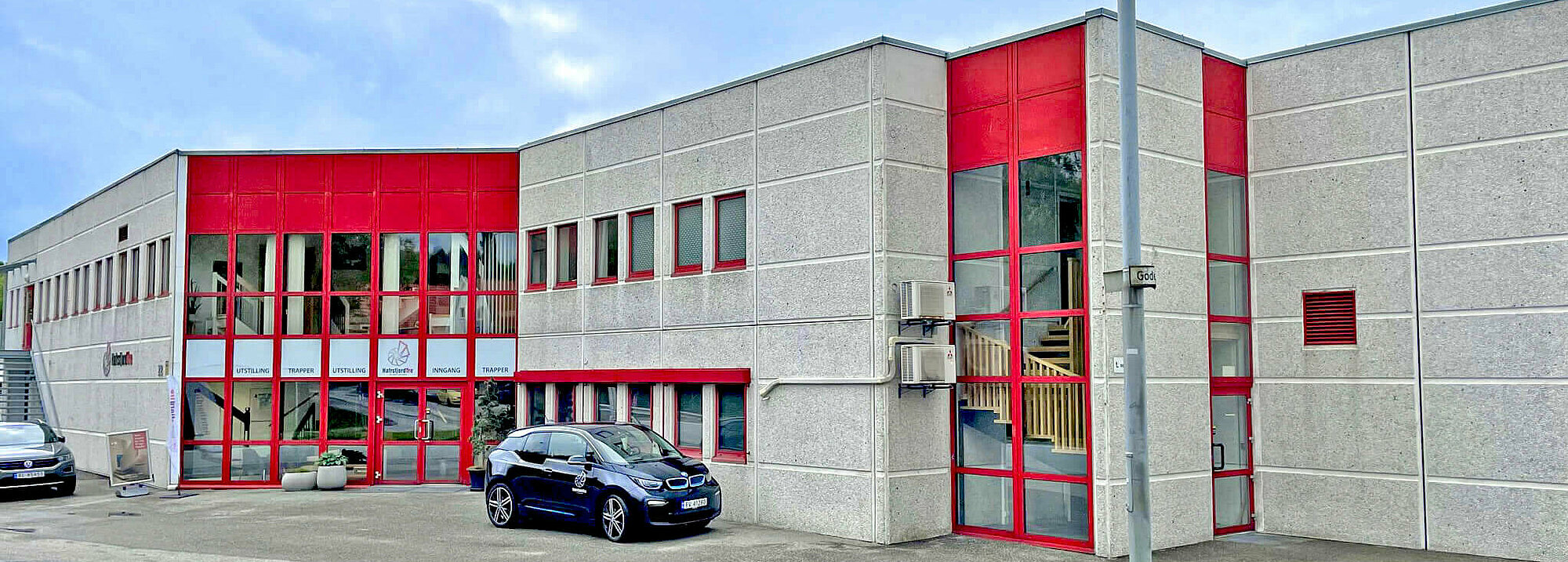
The stair builder Hafrsfjord Tre A/S was founded in Stavanger, Norway in 1977. The company has been using Compass Software to optimise their stair production since the early 1990s. Back then, the company was still designing stairs in DOS and printing the stair parts on paper to manually cut them out.
Hafrsfjord has always been an innovator and so they added their first CNC machine as early as 1999. Soon another followed and they have been working very successfully with 2 machines ever since. Throughout 30 years, Arvid Hebnes, owner of Hafrsfjord Tre A/S, has always been very happy with Compass Software and relied on their cutting-edge technologies to improve his production.
You can read the entire case study in PDF format here: Download
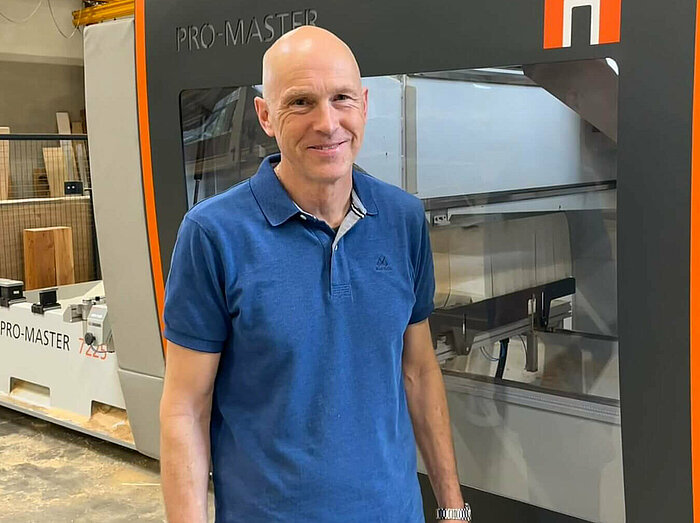
Implementation of a New Automatic Warehouse with Nesting Machine
Not too long ago, Arvid Hebnes saw an innovative system at another Norwegian stair builder and knew he wanted to implement a similar system in his own workshop. The idea was to install an automatic crane that would store material automatically as well as load plates onto a nesting machine that would automatically process parts and even finish them completely, if possible.
Today, Hafrsfjord is working with a Compass-Software-controlled crane that automatically stacks plates into 5 piles made of the same size and material.
Once, the CAD drawing of the stairs has been cleared for production, the operator scans a barcode that contains the respective work processes, and the CNC code is generated at that moment with the most current machine information. Compass Software then tells the system what kind of material is needed, and the crane automatically loads a plate of that material onto the conveyor belt. The crane corrects the positioning so that the plate can be transported to the nesting machine. The Holzher Dynestic 7535R nesting machine with 5 axes automatically pulls the plate onto the worktable using vacuum cups. The machine then processes the parts with the plate optimisation module and finishes them, if possible, completely. After the milling process is completed, the operator prints a barcode label for each individual part so that each part can be easily identified at any time by simply scanning it. Any parts that require post-processing can be transported to their 5-axis Holzher ProMaster 7225 CNC machine and the work processes can be generated via the barcode scanning.
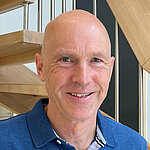
I cannot name specific results of the work process change yet, since the system has only been running for about a month. I am expecting to see an increase in stair production from about 650 stairs a year to over 900 per year. Ultimately, I think it will be possible to produce 50 % more stairs with the same number of employees thanks to the new system. Furthermore, I can already see material savings of 10 – 15 % due to the nesting machine’s efficiency.
Arvid Hebnes - Owner
Less Manual Labour and More Interesting Work
The new system also has several advantages for the Hafrsfjord employees. Before the heavy wood plates had to be lifted and transported manually. This is now done automatically by the crane. Even though the new work process is a big change and requires additional training, it also makes the workplace more interesting for the workers and they can develop new skills. Some employees are able to transition to other business areas, such as sales or other places in the workshop, as less manual labour is needed at the machine. All in all, the new work process is a positive and efficient change that makes the workshop more future-proof.
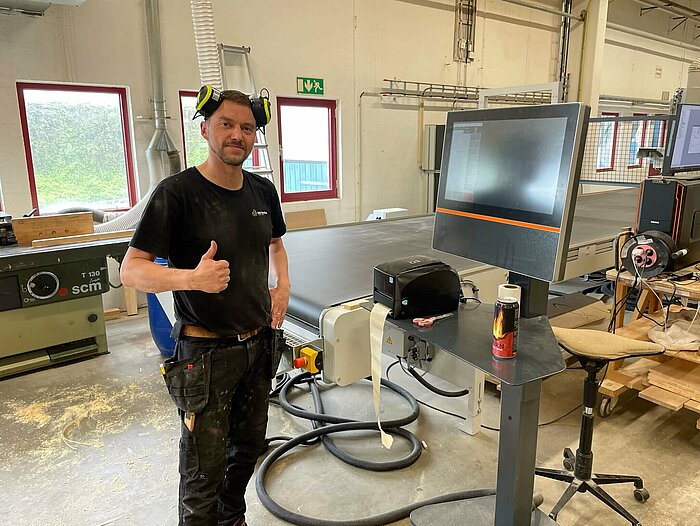
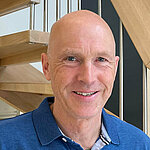
I have always been very satisfied with Compass Software for the last 30 years. I especially appreciate the personal connections I have made at Compass. I have been able to work with great people in sales and development. I feel 100% supported by the Compass support team and enjoy the personal touch.
Arvid Hebnes - Owner
Future Projects with Compass Software as Strong Partner
Arvid Hebnes is excited about the advantages the new system brings to compete in the market. The stair builder will be able to produce more stairs, more quickly, with the same number of employees. For the future, Hafrsfjord is looking at the MES system PROKON. The biggest problem right now: “We need to find more people to assemble all these additional stairs we can produce now!”