New Installation at Jenniches Stairs
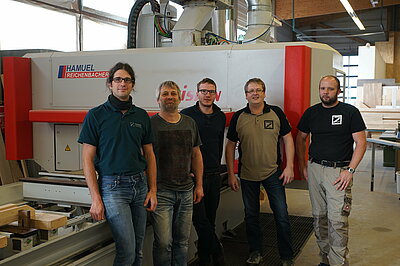
All in all the entire installation went smoothly. The team compiled of Jenniches employees and the Compass Software technician milled many test parts. Furthermore, they configured the standard parts’ predefinitions for 4 staircase types: closed staircases, open staircases, bolted staircases and folded staircases. The entire production for these staircases is controlled with the new Windows interface that Compass Software offers. Most of the manual labor that was necessary before, has become obsolete, since Jenniches is now able to process all parts on the 5 axis CNC, such as the placing of angled drillings in closed treads, which had to be done manually with a special drilling machine before the installation. Furthermore, before switching to Compass the stair builder had to invest an entire workday into programming fittings for folded staircases in an external CAD system. Now, all drillings and details are generated with only one click in the CNC program. This saves time and money.
At a first glance the Jenniches team thought that constructing with Compass Software was much more complicated than before because the system offers so many details, however, they realized quickly that they had finished so many more things already after going through the initial construction: the CNC code is generated automatically, the program creates 3D pictures for the customer, forms are calculated automatically, measurements and parts lists are available right away. The biggest profit is expected to come from CNC processing, since the initial completion level of the parts will be much higher because of the specific steps taken to optimize fittings and predefinitions in the construction and post-processor. Elaborate programming through DXF drawings and external CAD/CAM systems during the planning process, as well as most manual labor in the workshop itself, have become obsolete. The new system reduces error sources and simultaneously improves the quality of the parts produced, all while saving time. Workers, who previously had to do manual touch-ups are freed up and can be utilized in other ways, which increases productivity and the number of stairs that can be finished. All in all the team feels positive about the change and wants to work together again in the future. Until then we want to wish Jenniches much success and we are looking forward to the next project.