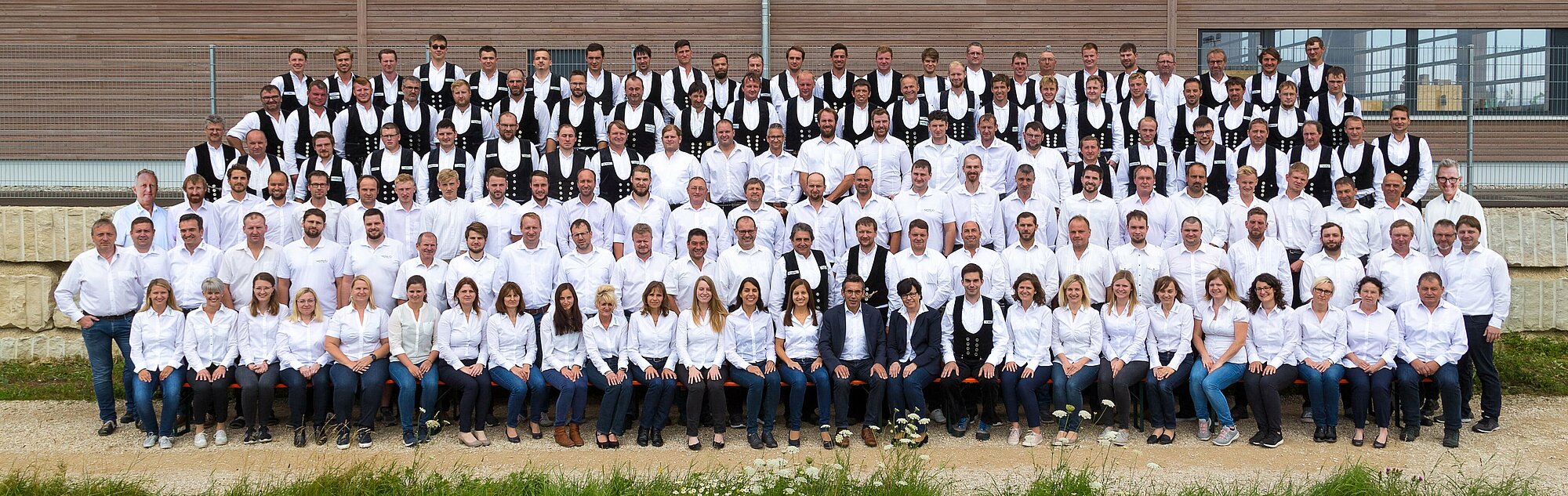
© Taglieber Holzbau GmbH
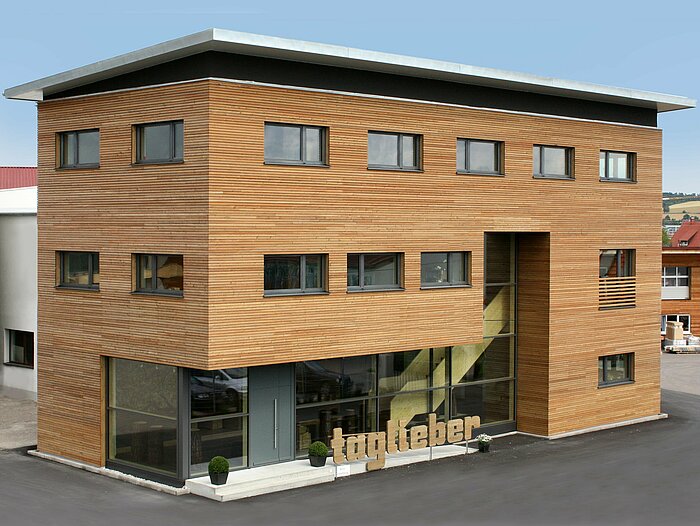
© Taglieber Holzbau GmbH
The fourth-generation family company Taglieber Holzbau GmbH from Bavaria, Germany is producing wood components for private and commercial buildings, frame carpentry, and stairs. Since 2019, the company, who employs over 200 workers, has been using Compass Software to control their 5 axis SCM Accord 40 FX, which cuts especially precise. The woodshop processes stair components and building facades on the CNC machine. For their stair production, Taglieber uses Compass Software´s CAD/CAM complete stair software. The woodshop’s timber department creates CAD designs with the Dietrich´s 3D software system and converts CNC processing data via the Compass Software BTL interface.
You can read the entire case study in PDF format here:
Custom Stair Designs – The Easy Way
Taglieber Holzbau exclusively focusses on custom-made stair designs. Before switching to Compass Software, the woodshop was using the Wagemeyer stair software. After a thorough search for a replacement, the company decided to control their newly purchased CNC machine with Compass Software. Taglieber also uses the laser measurement system Flexijet to record building-site measurements. Due to the integration of the Flexijet system in Compass Software, all data is easily transferred to the design tool. Once the CAD design process is finished, Compass Software automatically generates all CNC codes and transfers them to the SCM processing centre. Taglieber produces ca. 140-150 custom staircases annually. The CAD/CAM all-round solution gives the woodshop a lot of flexibility and enables them to realise highly customised stair designs.
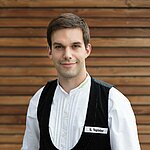
The import of Flexijet stair measurements works really well. Once imported, we already have the correct measurements, so all we need to do is adjust the CAD design and some details. Ever since we started using Flexijet with Compass, our stairs are significantly more precise, and we are able to cater to more specific customer wishes.
Stefan Taglieber - CEO
Precision CAD Software Implemented in CAM
The high precision of the SCM machine enables the company to produce different building façade components that were too complicated to manufacture by hand or had to be purchased externally before. Conventional joinery machines do not cut with enough accuracy to process post-and-beam constructions for example. Post-and-beam constructions are used for glass fronts on building facades. Vertical posts are connected to horizontal beams and thus, form a sturdy and bearing framework. “Our architects are able to draw the parts with the exact measurements since they know the maximum length capacity of the CNC machine. This makes the entire process extremely smooth, efficient, and flexible. Back in the day, we almost never produced these constructions since they were too hard to make by hand. Now, we can easily manufacture them on the SCM. Manual post-processing has become absolutely unnecessary,” explains Stefan Taglieber.
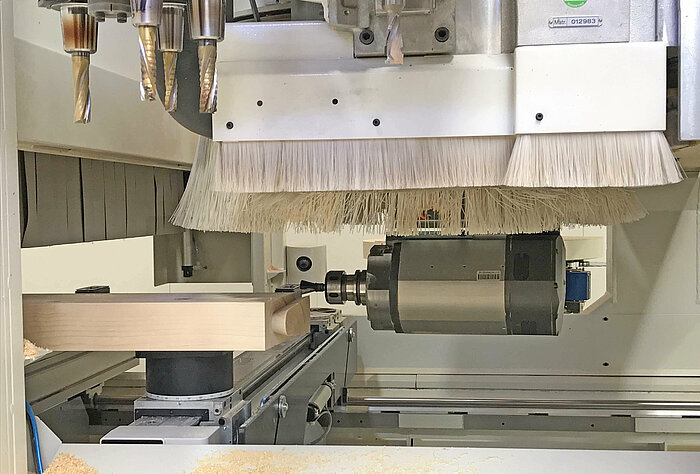
© Taglieber Holzbau GmbH
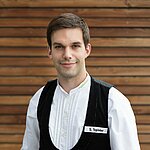
Due to the fact that different CNC processes are computed with one software, our employees only have to be trained in one software as well. The user interface of the BTL processor is designed very clear and simple. In case we have questions, we always know who to contact. It is great to only have one point of contact for all questions, whether it´s for stair building or timber.
Stefan Taglieber - CEO
Integrated CAM Production with One Software
One major advantage for Taglieber, is the utilisation of one CAM software for several production areas. The Compass Software postprocessor automatically transfers all CAD data from the Dietrichs´s system to the CNC machine. Furthermore, all stair CAD data is also directly sent to the CNC machine via Compass Software. The advantage is that each specialty department can use their own “expert program,” but both can transfer CNC code easily – the stair production team directly, and the timber team via the Compass Software BTL processor.
The integrated Compass Software solution enables the woodshop to process different parts on only one machine. Depending on the utilisation rate and the volume of orders, it is possible to alternate between the production of stair parts and timber components. The best thing is, there is no switching between different software. Everything runs smoothly and uniformly.
Future-Proof Perspective
Compass Software gives the house builder a clear advantage over the competition. Some components, such as the popularly used post-and-beam constructions for building facades, were not possible to produced efficiently before. Timber components like these are now child’s play. In the future, Taglieber plans to produce even more timber components on the CNC-machine and expand this area of their business even further.